“What’s your company’s climate footprint?” It’s a hot question these days — one being asked increasingly of companies by customers, investors, activists, regulators, and others.
OK, it may not be exactly that question, but it’s probably in some form, like, “What’s your company doing to reduce its climate impacts?” Or, “How do you call yourself environmentally responsible when you take so damn many plane trips?”
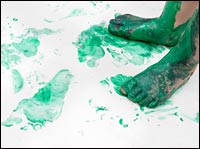
Photo: iStockphoto
Whatever the question, providing an answer will require understanding what, exactly, your company does to contribute greenhouse gases into the atmosphere. And therein lies a challenge: Calculating a company’s climate footprint (sometimes referred to as a “carbon footprint”) is far from simple. To begin, there are the sheer number and range of business activities that must be tracked: facilities, operations, transportation, travel, and purchases of everything from raw materials to office supplies.
Beyond that are complex questions of where to draw the boundaries: how far upstream and downstream your company must count. For example, are you accountable for the greenhouse-gas emissions related to extracting and processing the raw materials or energy you purchase for your operations, or are they your suppliers’ responsibility? When your employees travel by air, are you or the airline responsible for counting and reporting the climate-related impacts? What about downstream: Who should account for the climate impacts of customers using and disposing of your products?
On top of all that, how do you ensure that this information is collected consistently so it can be aggregated for different departments, facilities, business units, product lines, and geographic regions?
Answering such questions can require the wisdom of Solomon — and the patience of Job. Fortunately, there is growing consensus about how to measure and track greenhouse-gas emissions.
Good thing. Companies seem to be increasingly tripping over themselves trying to put on a friendly climate face. Each month brings new reports of companies making commitments to reduce or offset some part of their climate footprint. It’s hard to attend an environmental event these days without hearing that the event, including all participants’ travel, has been rendered “climate neutral” (or some such moniker; there are several variations on this theme). Even rock bands, from Pearl Jam to Dave Matthews, are drumming out the climate impacts of their concerts and tours.
So, how do you measure your firm’s carbon footprint?
Measure Twice, Cut Once
Start with the basics: Your offices and how you get to and from them each day. If you’re a small or mid-sized organization, energy use and transportation probably represent a good chunk of your impacts. There are simple online calculators, like the one offered by the U.K. group Climate Care, that can give you an instant measure — though gathering all of the information needed for even this simple calculator likely won’t be instant. (Keep in mind that many of these free calculators’ creators want to sell you climate offsets, which allow you to “neutralize” your emissions by purchasing renewable-energy credits and other things.)
Next, take a look at the rest of your operations — what you buy, sell, and make. To calculate the climate impacts, you’ll need to find carbon or greenhouse-gas emissions data for these things. This is where you’ll need some outside help from consultants or other experts.
“The first comprehensive footprint that we did in 1999 measured facility energy, finished-product distribution, incoming supplies, employee commuting, and work travel, and we chose a few key items in our supply chain that we intuitively thought would have high emissions — our yogurt cups and the milk production,” says Nancy Hirshberg, vice president of Natural Resources for Stonyfield Farm. She notes that while there is a lot more information available today than in 1999, the process hasn’t changed much. “There are still a lot of assumptions that need to be made. Footprinting is still far from an exact science. But we definitely end up with a very clear picture on where our greatest impact is and where we need to focus our efforts.”
Stonyfield is one of many companies that have worked with Portland, Ore.-based Trexler Climate + Energy Services, one of the pioneering firms in the climate arena. “If all you’re doing is tallying up your gas and electricity use, it is about a seven-minute operation, not a big deal,” says Mark Trexler, president of the company. The bigger deal, he says, comes when you attempt to comply with the GHG Protocol Initiative, the globally recognized reporting standard for greenhouse-gas emissions.
According to the protocols, companies must choose how to account for direct and indirect emissions. Direct emissions are those from sources owned or controlled by your company — for example, emissions from factory stacks, manufacturing processes and vents, and company-owned or leased vehicles. Indirect emissions are a consequence of company activities, but occur from sources owned or controlled by others — such as emissions from the production of electricity you purchase, contract manufacturing, employee travel, and emissions from using the company’s products.
Suffice to say, it can get complicated quickly. The GHG Protocol is intended for larger companies, so if yours is a smaller operation, or a service company with no factories or other industrial operations, it probably isn’t worth going through it.
Why bother at all? A well-designed emissions inventory can serve several business goals, including helping your company improve its efficiencies, reduce costs, and get public recognition for taking action to reduce or eliminate your climate impacts. Addressing climate change may also affect your company if it is part of a larger supply chain. Some small businesses serve larger organizations and companies that must calculate and manage both direct and indirect greenhouse-gas emissions. Many major corporations now seek suppliers with a demonstrated commitment to minimizing their climate impacts, as this impact adds indirectly to their own.
Stonyfield’s efforts to measure its emissions makes for a good case study that may help your company understand the process. In 1996, the yogurt maker committed to offsetting 100 percent of the carbon dioxide emissions from its production facility’s energy use by the year 2002. The company published an “Environmental Cookbook” describing the successful project.
Trexler emphasizes that for most smaller companies, measuring and tracking climate impacts is a fairly simple proposition. “It’s certainly not rocket science. It’s being able to track down the right conversion factors for your company. There are a lot of people around right now who do that.”
More important, he says, is to understand why you’re doing this in the first place. “Is the inventory the end or the beginning?” he asks. “If it’s the end, then what was the point? If it’s the beginning, that’s a very good thing. It opens up a lot of possibilities, like education, offsets, and trying to spread the word in order to influence policy makers and others.”
Count On This
ClimateBiz.com offers a special section on climate management for smaller companies, including a backgrounder, best practices, and links to organizations, tools, and other resources. There are also a variety of other online carbon calculators intended for companies. Two of the best are from the Climate Neutral Group and the Australian firm Climate Friendly.