There are only four companies that manufacture polysilicon, a critical material for solar panels and semiconductors, in the United States. This spring, one of them got a big influx of cash. In April, a Korean company called Hanwha Solutions announced it had become the largest shareholder of REC Silicon, which can produce 16,000 metric tons of polysilicon annually from a refinery in Washington State—enough to meet more than a quarter of the U.S. solar industry’s demand. Hanwha, which already operates the largest U.S. solar panel factory in Georgia, described the acquisition as part of a plan to “revitalize the U.S. solar market” by creating a made-in-America supply chain from raw materials to finished products.
If that plan is successful, it would not only demonstrate the U.S. is, in fact, able to make solar panels with domestically sourced materials — a key policy goal of the Biden administration. It would also show that polysilicon refining, the most energy-intensive step in solar manufacturing, could be made considerably greener in the process.
In the pantheon of climate solutions, low-carbon polysilicon may not sound particularly sexy. But it has become a hot topic in the world of solar as corporations and governments start thinking seriously about how to drive their emissions all the way to zero, including in the so-called upstream supply chains that provide materials and components for renewable energy. Already, solar photovoltaic, or PV, panels generate among the lowest carbon emissions of any energy source out there over their entire life cycle, including manufacturing. But as the industry grows, even the relatively small emissions associated with manufacturing PV panels could become significant in aggregate, potentially peaking at levels comparable to the current yearly emissions of large industrialized nations like France or Germany.
A recent study found that in a scenario where the world deploys solar rapidly, PV production could lead to 25 to 30 billion tons of cumulative carbon dioxide emissions by the middle of the century, eating up roughly 10 percent of the remaining carbon budget for limiting global warming to 1.5 degrees Celsius (2.7 degrees Fahrenheit). If we don’t rapidly embrace renewables like solar, we have little chance of meeting that climate target. Still, it is possible to increase our odds by cleaning up polysilicon production, which accounts for roughly half of the climate impact of solar PV.
REC Silicon is showing how the industry might do that. The company’s polysilicon production facility in Moses Lake, Washington, uses low-emissions hydropower from the local electric grid, instead of the coal that’s often used to power polysilicon refineries in China. What’s more, instead of using the energy-intensive process to purify silicon that’s standard in the industry, the Moses Lake facility has pioneered the commercialization of an alternative process that REC Silicon claims uses up to 90 percent less energy.
The Moses Lake facility has been closed since 2019 due to Chinese import tariffs that priced the silicon maker out of the solar market. Now, thanks to Hanwha’s investment, REC Silicon has begun the process of bringing the facility back online.
“We have a very stable, low cost of power to produce polysilicon that’s also very low carbon,” REC Silicon CEO James May told Grist. “And that’s what we want to do.”
To understand why polysilicon manufacturing produces emissions, you have to understand how it works. Originating from quartz, a humble, abundant mineral, polysilicon is a highly refined form of silicon that converts sunlight into electrons inside a PV panel. To make it, manufacturers heat quartz in a furnace to produce metallurgical-grade silicon, which is about 99 percent pure. Typically, metallurgical-grade silicon then gets transformed into a gas, which is released into a superheated reactor where it resolidifies onto seed rods as polysilicon, a form of silicon upwards of 99.999999 percent pure. This process, known as the Siemens process, is how more than 95 percent of polysilicon is refined around the world today, according to the clean energy research firm BloombergNEF.
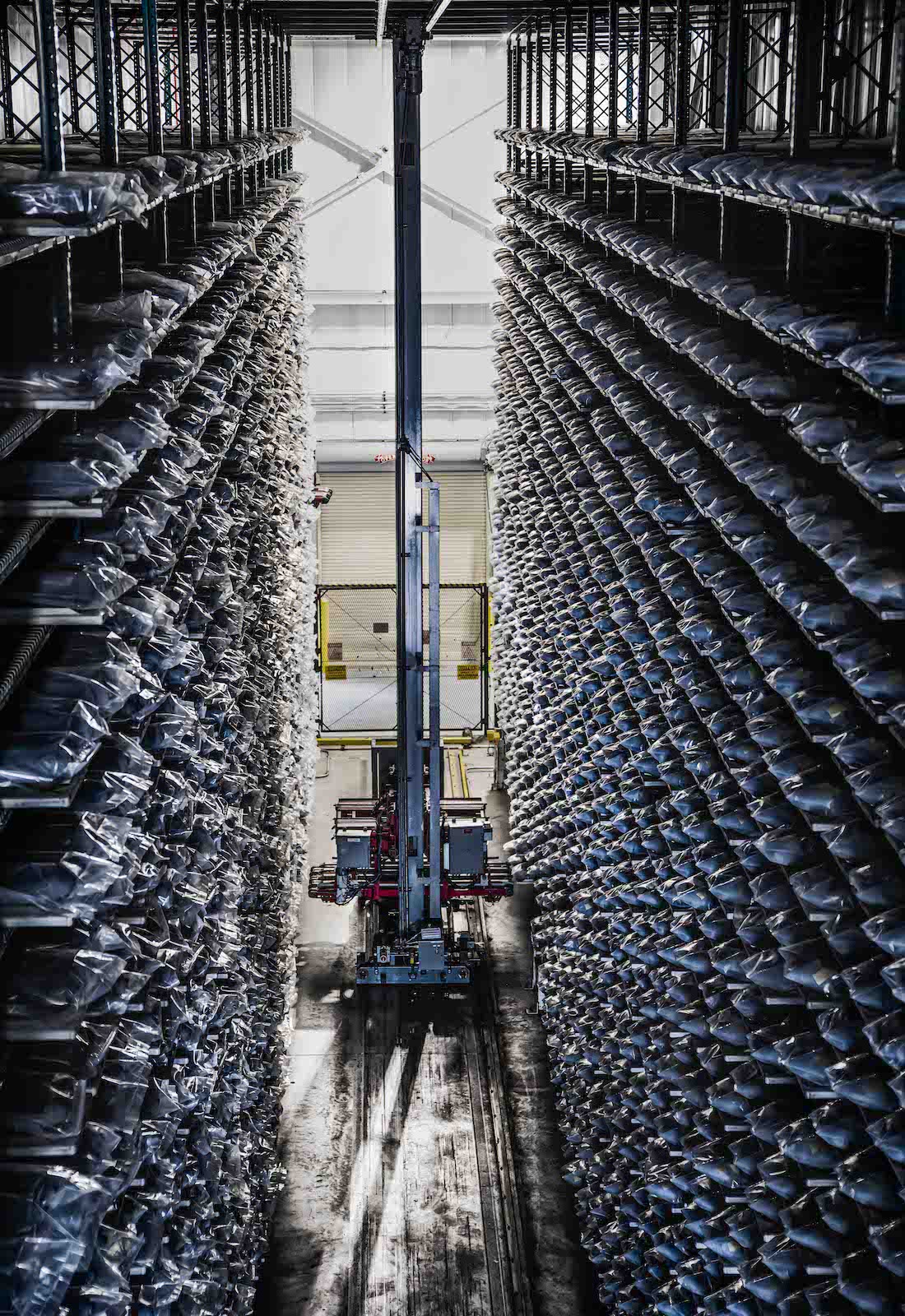
While the Siemens process has been around for decades and is considered the most reliable way to refine polysilicon, it has a downside. As the silicon rods are forming at the center of the reactor, the reactor walls need to be kept cool to prevent the silicon from crystallizing there. Maintaining that temperature difference is “really energy intensive,” Jenny Chase, who heads solar analysis at BloombergNEF, told Grist. To make polysilicon affordably, companies set up their refineries in places with access to cheap and abundant electricity. In China, where 78 percent of global polysilicon production occurred last year, this means regions where the electric grid includes lots of coal.
“Most people are very aware of what happens with solar once it’s put in the field — that it generates zero-carbon electricity,” said Michael Parr, the executive director of the Ultra-Low Carbon Solar Alliance, an industry group focused on driving down emissions across the solar supply chain. “Most people don’t know that upstream, in manufacturing, there can be quite high carbon emissions, particularly in the Chinese supply chain.”
One way for the solar industry to clean up this supply chain is through improvements in manufacturing efficiency. This is already happening: Data shared by BloombergNEF shows that between 2014 and 2019, the amount of electricity needed to refine a kilogram of silicon declined 22 percent. At the same time, the silicon content of solar panels is falling as manufacturers continue to make solar cells — the individual, wafer-like pieces of silicon inside a solar panel — thinner and lighter. And the efficiency of those cells, or their ability to convert sunlight into electricity, is steadily rising.
“The efficiency of the solar cells has improved by about 50 percent in the last 25 years, and amount of silicon we use is cut down by a factor of two or three,” Meng Tao, a solar sustainability researcher at Arizona State University, told Grist.
Greater efficiency means less energy and emissions are expended to manufacture a solar panel. Further climate gains are possible if manufacturers power their operations renewably. Right now, U.S. electric grids tend to be less carbon-intensive than their Chinese counterparts, meaning there’s a good climate case for onshoring the energy-intensive steps like polysilicon production. That hasn’t escaped the Biden administration: In a February report on the solar supply chain, the U.S. Department of Energy, or DOE, identified ramping up polysilicon refining as the top thing the U.S. could do to secure a stable solar supply chain. Such an industry, the DOE noted, could take advantage of low-emissions hydropower in the Northwest and elsewhere.
“Economics is on our side here,” Garrett Nilsen, acting director of the Solar Energy Technologies Office at DOE, told Grist in an email. “Hydropower is one of the cheapest forms of electricity in the country, so polysilicon producers naturally locate their plants accordingly.” The DOE, he said, is also investing in programs to deploy additional wind and solar power more cheaply around the country, potentially creating new renewable energy hotspots where polysilicon makers could set up shop.
When it comes back online, REC Silicon’s Moses Lake facility will use hydropower produced on Washington State’s Columbia River to produce polysilicon for solar panels. The largest U.S.-based polysilicon manufacturer, Hemlock Semiconductor, produces polysilicon for both the solar and the semiconductor industry in Hemlock, Michigan. There, the electric grid already includes a significant amount of hydroelectric storage capacity, and it’s getting steadily cleaner as the local utility phases out coal and brings more solar energy online. Hemlock solar commercial manager Phil Rausch told Grist that per kilowatt-hour of energy used, the emissions associated with the electricity the company purchases are about half of its competitors’ electricity emissions.
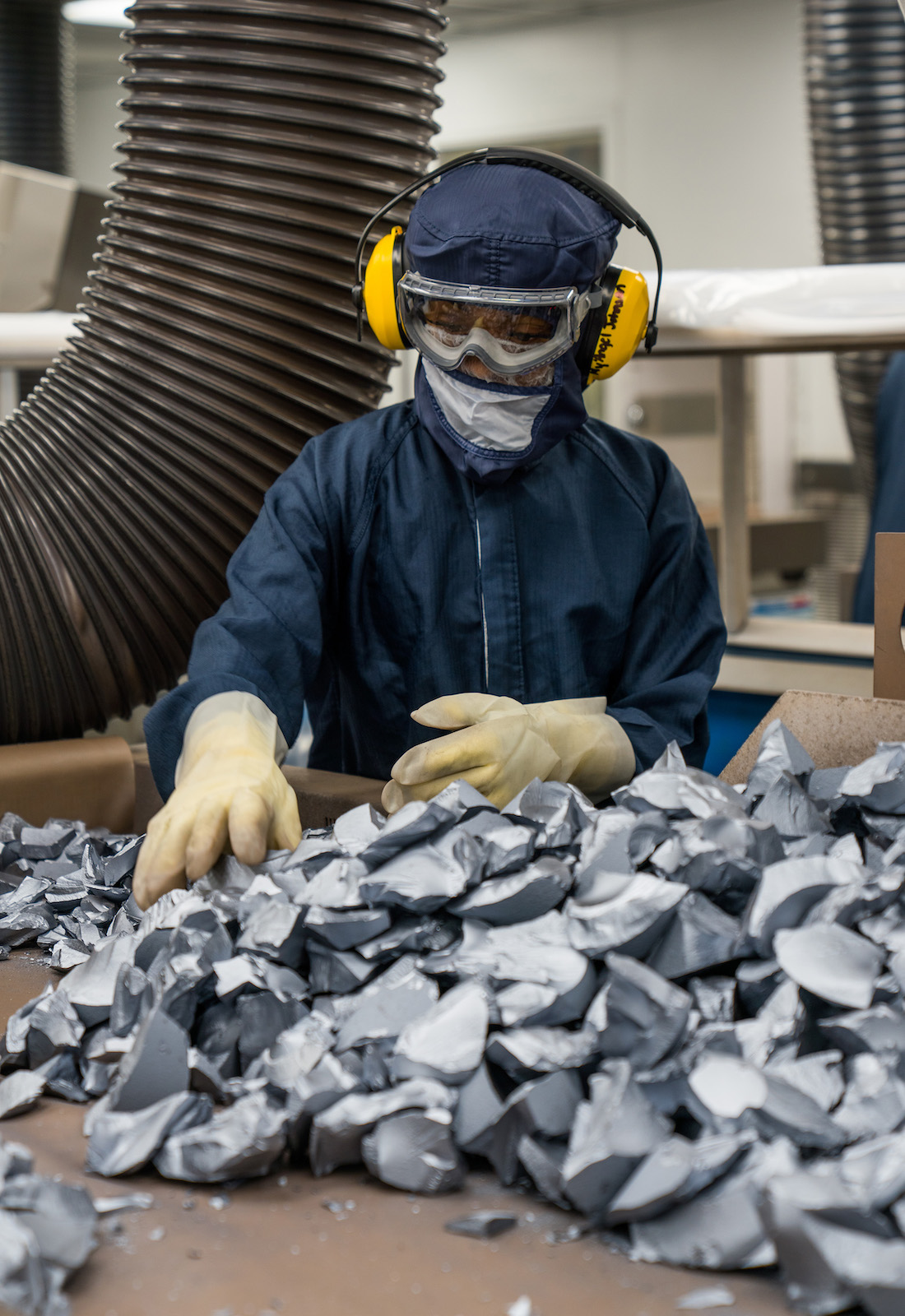
Beyond improvements in manufacturing efficiency and getting power from greener grids, a handful of polysilicon makers have turned to alternative processes that are less energy intensive than the Siemens process. Chief among those is the so-called “fluidized bed reactor,” or FBR, process REC Silicon uses at its Moses Lake facility. Hot, silicon-rich gas is fed into a chamber containing pellets of silicon, which grow in size as more silicon crystallizes on them. Because heat is introduced from outside the reactor, no cooling is required, allowing considerable energy and cost savings, according to May.
Industry experts say it is more difficult to produce ultra-high-purity polysilicon with FBR technology compared with the Siemens process, limiting its adoption in the industry. Rausch of Hemlock said that his company investigated the FBR process “extensively” over the last decade but ultimately determined that the polysilicon it produced “did not meet the needs of the industry.” May, however, is confident that REC Silicon can use the method to make polysilicon that meets the increasingly stringent purity requirements of solar manufacturers thanks to a series of recent upgrades to its Moses Lake facility.
Parr of the Ultra-Low Carbon Solar Alliance is cautiously optimistic. FBR “is a more difficult technology to get better purity from,” he said, but REC Silicon has spent years improving its process. “I think like any technology, it takes a while to perfect it, but it is inherently lower energy, lower carbon technology, so that’s promising.”
Any polysilicon maker that can deliver a greener product — whether that’s due to more efficient production methods or cleaner power sources — is likely to have a growing advantage in the solar market as companies or governments start paying more attention to supply chain emissions.
“We’re already seeing the downstream buyer becoming much more sensitive to the embodied carbon in the supply chain,” Rausch said. As an example, he notes that several years back, when France began taking the carbon footprint of solar panels into account in its public procurement process for clean energy, companies buying polysilicon from Hemlock started doing better in that market. New labeling schemes, like an eco-label for solar that the Global Electronics Council is developing in partnership with the Ultra-Low Carbon Solar Alliance, are likely to drive further interest in clean polysilicon.
Efforts to make solar manufacturing more sustainable shouldn’t detract from the need to deploy solar power as quickly as possible, says Garvin Heath, an energy sustainability researcher at the National Renewable Energy Laboratory, or NREL. Across the entire life cycle, NREL researchers have found that solar PV already generates 10 to 20 times lower carbon emissions than fossil fuel energy sources like gas and coal. Solar is already a critical tool for fighting climate change, regardless of manufacturing emissions.
At the same time, the industry should do everything in its power to keep its emissions as low as possible, considering how little carbon we have left in the bank to avoid crossing dangerous climate thresholds.
“We shouldn’t stop deploying PV because we want to make it better,” Heath said. “We should deploy as much as possible and make it better.”
