Dear Umbra,
Sustainably grown bamboo is a very good choice for fabrics. But how does the consumer know it is harvested sustainably? After all, some bamboo is clear cut from old-growth stands. Even in cultivated bamboo there are some very unsustainable practices (for instance, harvesting too young). How can you know if the bamboo fabric you are buying is harvested sustainably?
Gar L.
Olympia, Wash.
Dearest Gar,
Telepathy is the only way. Close your eyes, put your hand on the fabric, and let a vision of a Giant Panda come in to your mind. If the panda is frolicking, all is well.
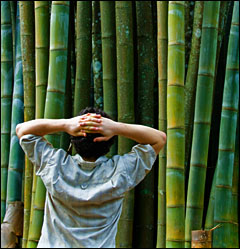
Dude, that’s a lot of grass.
Bamboo is hot hot hot, for flooring, fabric, and myriad other stripy items. It is an inexpensive material, and the plants grow quickly and can do so without many fertilizers or pesticides. The mysteries of the exploding bamboo industry include the questions you mentioned above, and others such as how are the workers treated, are commercial pressures leading to the removal of other vegetation and the planting of bamboo in its place, are farmers adding chemical fertilizer to increase production, and what toxic chemicals are added in order to make products such as flooring and fabrics?
We’ll get to that last question in a moment. The answer to the rest is: no one really knows for sure. I spoke with Jackie Heinricher, a bamboo expert and entrepreneur here in Washington, who says bamboo is both blessed and cursed: It’s a truly green plant, but there’s no accountability in the current industry.
There is no sustainable-harvest certification to look for, in part because, says Jackie, bamboo grows so quickly that no one imagined it would ever have overharvest issues. I did find that the Forest Stewardship Council has a certified bamboo flooring producer. I also tracked down one organic bamboo fabric producer, certified by OCIA International and the USDA, whose products are sold by Bamboosa and perhaps others. (The organic certification process for bamboo fabric would be similar to that for other fibers such as cotton, and is governed by crop and livestock production standards.) Another certification often touted for fabrics is Oeko-tek 100, however this only guarantees minimal residue on the fibers and tells us nothing about raw material production methods.
Outside of these eco-certifications, I think there is no surety for sustainably produced bamboo fabric. Given the general positives about bamboo — its speedy regrowth, its low fertilizer needs, its high carbon-sequestration abilities — we could hold out some reasonable hope that a bamboo plant’s life was fairly low-impact. But here’s the catch: It’s the bamboo fiber production that leaves quite a bit to be desired.
It’s just difficult to make a hard grass into a shirt, and so we use chemicals to soften the fibers. Here’s what I’ve read: there are two ways to mash a bamboo plant in to fibers appropriate for fabric. One is mechanically, via crushing and enzymes. Mechanical processing results in a linen type of fabric, and is expensive and unusual. Most bamboo is processed in a bath of lye and carbon disulfide, along with something referred to as “multi-phase bleaching.” It is akin to the method for making rayon out of cellulose, and it can be quite toxic to workers and nearby nature.
So is bamboo worse than other fabrics? Probably not. It may in fact be a little better. There aren’t good “chain of custody” certifications, but that doesn’t mean that the wool is pulled over our eyes and bamboo is never ecologically preferred. A possibly promising development comes from Jackie and others, who are finding ways to cultivate bamboo domestically and responsibly. Meantime, we’re just stuck with our same old clothing rules: buy few, buy organic, buy used, dry on the line.
Pandaly,
Umbra