This story was originally published by Canada’s National Observer and is reproduced here as part of the Climate Desk collaboration.
It’s been almost a decade since Jocelyn Doucet first experimented with recycling plastic waste in a microwave.
Now he says the technology derived from those early efforts will make it possible to produce plastic almost exclusively from recycled materials.
“We’re consuming more and more plastics,” says the Quebec-based engineer and founder of Pyrowave, a company pioneering microwave-based plastic recycling technology. “Yet there are not that many solutions to address the end-of-life problem, and this is what we’re proposing.”
The technology is so promising it has caught the attention of French tire giant Michelin. Last year, the company announced a partnership with Pyrowave to build a microwave recycling system for tires. It will be the first time Doucet’s technology is used on a commercial scale.
Most recycling in Canada today is mechanical, where plastics are shredded before being melted down to make new, usually lower-quality, products. For the process to be viable, the stream of plastics entering the processing facility needs to be clean and well sorted, which poses huge logistical challenges. Pyrowave’s technology then uses high-powered microwaves to break clean polystyrene — a common plastic used to make everything from yogurt cups to keyboards — into molecular components, or monomers, that manufacturers can use to create entirely new polystyrene plastic.
Simple as it sounds, the approach is novel. Few researchers had successfully used microwaves to break plastic into its constituent parts until Doucet, who has a Ph.D. in chemical engineering from the Polytechnique de Montréal, took up the challenge with a team in 2009.
At the time, he was working on food waste technologies and wanted a new challenge. “We started getting approached for plastic waste,” he says. Plastic recycling was something new.
He wondered if pyrolysis could be used in the recycling process. Pyrolysis is a chemical process that burns carbon-based materials like wood or plastic without oxygen to remove the material’s hydrogen and oxygen molecules, leaving nothing but carbon. It’s ancient — Egyptians used pyrolysis to make charcoal.
Doucet thought a modified version could be used to recycle plastic.
“Very quickly, we fell on a microwave unit in the lab and started playing with microwaves,” he said. They found high-powered microwaves worked — an exciting discovery for the environmentally minded team.
Doucet’s microwave process uses electric energy instead of heat, dramatically reducing the amount of energy and greenhouse gas emissions (GHG) needed to produce polystyrene plastic, he says. According to a forthcoming life cycle assessment by Pyrowave, producing polystyrene using microwave pyrolysis recycling is 40 percent more energy efficient than virgin oil production, Doucet adds.
Observers are reserving judgment.
“Pyrowave’s technology might play a role in terms of displacing the production of virgin plastic and materials, but until we have more transparent and verifiable data on the yields, environmental and climate impact, we need a cautionary approach,” says Shanar Tabrizi, chemical recycling and plastics-to-fuel policy officer for Zero Waste Europe.
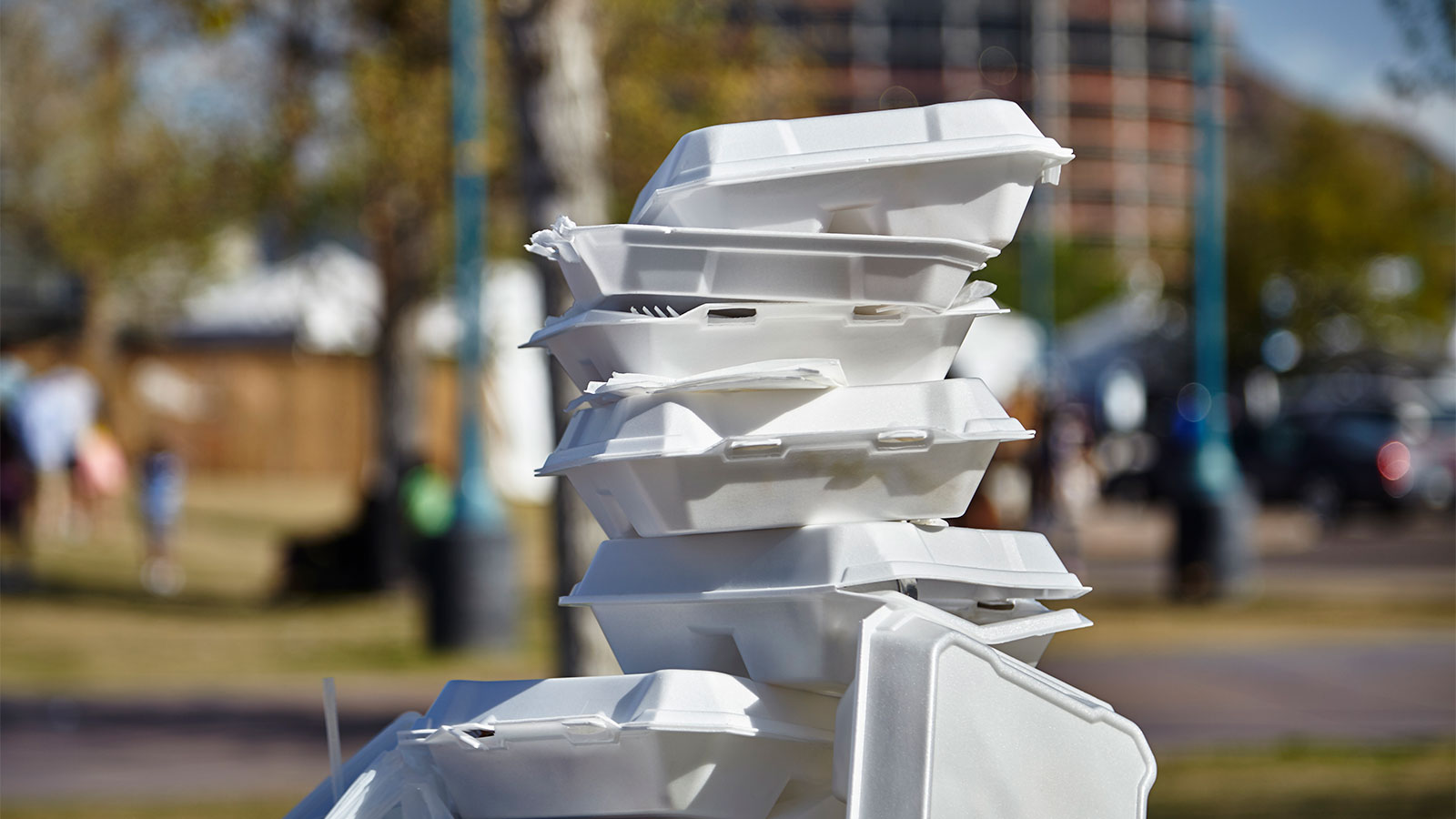
Those potential impacts are broad, from the energy required to collect, sort, and clean plastic waste before the recycling process to managing the toxic residues created by plastic additives. She also noted life-cycle assessments can be misleading, depending on their methodologies.
“It’s hard to assess (Pyrowave’s) claims and see whether there might be significant pollutants released in the process,” says Richard Heinberg, senior fellow at the Post Carbon Institute. “In general, anything we can do to recycle plastic in more environmentally friendly ways helps, but reducing the scale of production and consumption is even better.”
Maximizing the environmental potential of Doucet’s technology demands a wholesale restructuring of how we produce and dispose of plastics, the Quebec researcher said. New facilities that use microwave pyrolysis to manufacture plastic will need to be built. And as long as the price of virgin-oil plastic remains low, recycled plastic can’t compete. It will take government regulations mandating that new plastic products contain mostly recycled materials to make the switch, Doucet said.
He compared microwave pyrolysis recycling and virgin-oil plastic manufacturing to the difference between steam and electric trains. As electricity became widespread, train engineers quickly realized it was more efficient to build entire rail systems based on high-speed electric trains than it was to replace coal with electric heating coils in steam train boilers. The new technology pushed a wholesale shift in how rail systems worked.
“This is the opportunity to completely rethink,” Doucet says.
The petrochemical and oil and gas industries so far show no signs of slowing down.
Virgin-oil plastic factories have been integrated into oil and gas infrastructure like refineries and pipelines for decades — investments that industry is loath to abandon. The sector is betting on continued plastic production to stay afloat as the world transitions away from fossil fuels, with plastic manufacturing anticipated to fuel between 45 percent and 95 percent of the sector’s future growth. Fossil fuel and petrochemical companies are even spending $509 billion more worldwide to expand their facilities by 2024, according to a September 2020 report by the Carbon Tracker Initiative.
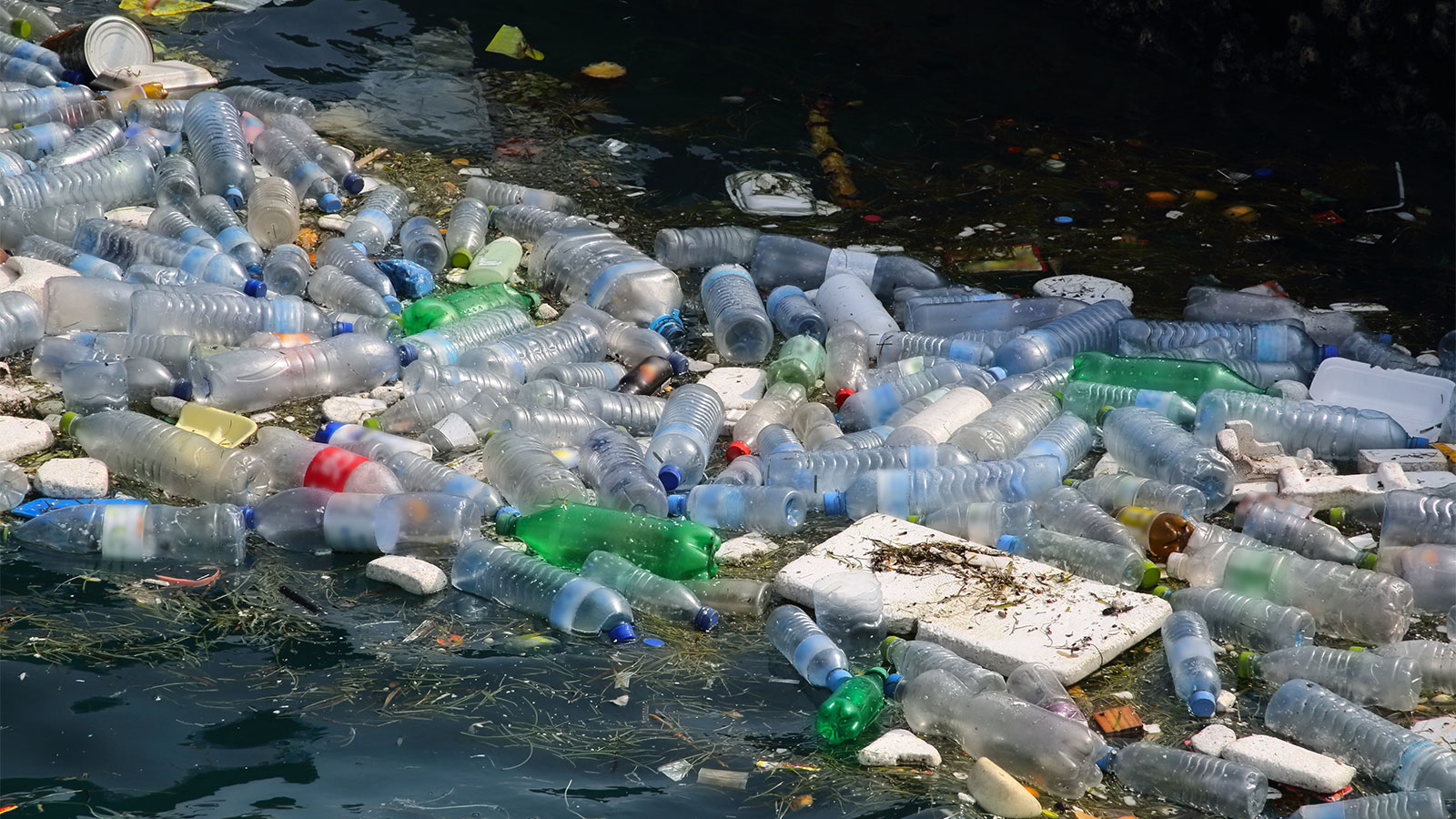
That has environmentalists concerned. While recycling — including microwave pyrolysis recycling — can be part of the solution, it can’t be used to justify current levels of production and plastic use, said Laura Yates, lead plastics campaigner at Greenpeace Canada. The organization has been leading efforts for greater government regulations to decrease overall plastic production and implement stringent recycling requirements in Canada.
In particular, Yates is concerned about efforts by the plastics industry to convert plastic waste into vehicle fuel. That will continue to stimulate virgin-oil plastic production and fail to reduce overall GHG emissions, Yates said.
Still, there are glimmers of hope. Virgin-oil plastic production decreased by four percent in 2020, and the trend is expected to continue in the coming decades, according to the Carbon Tracker Initiative. That shift is driven by more stringent rules in China and Europe mandating that plastic products be made primarily from recycled materials. They have also started to make recycled plastic economically competitive in those markets, Doucet said.
As well as the shift in Europe, the federal government is currently drafting new plastics regulations that could see similar policies implemented here, despite intense pushback from the plastics industry on key parts of the planned regulations. Doucet is hopeful that if the new rules are implemented, they will help make plastic recycling — including microwave pyrolysis recycling — commercially viable in Canada.
Doucet is honest about his technology’s limitations. It is only one tool to end the plastic crisis, not a panacea. Reducing how much plastic we use and ensuring what gets produced gets recycled more efficiently remain essential.
