At an abandoned coal mine just outside the city of Gillette, Wyoming, construction crews are getting ready to break ground on a 10,000-square-foot building that will house state-of-the-art laboratories and manufacturing plants. Among the projects at the facility, known as the Wyoming Innovation Center, will be a pilot plant that aims to takes coal ash — the sooty, toxic waste left behind after coal is burned for energy — and use it to extract rare earths, elements that play an essential role in everything from cell phones and LED screens to wind turbines and electric cars.
The pilot plant in Wyoming is a critical pillar of an emerging effort led by the Department of Energy, or DOE, to convert the toxic legacy of coal mining in the United States into something of value. Similar pilot plants and research projects are also underway in states including West Virginia, North Dakota, Utah, and Kentucky. If these projects are successful, the Biden administration hopes that places like Gillette will go from being the powerhouses of the fossil fuel era to the foundation of a new domestic supply chain that will build tomorrow’s energy systems.
In an April report on revitalizing fossil fuel communities, administration officials wrote that coal country is “well-positioned” to become a leader in harvesting critical materials from the waste left behind by coal mining and coal power generation. Several days later, the DOE awarded a total of $19 million to 13 different research groups that plan to assess exactly how much rare earth material is contained in coal and coal waste, as well as explore ways to extract it.
“We have these resources that are otherwise a problem,” said Sarma Pisupati, the director of the Center for Critical Minerals at Penn State University and one of the grant recipients. “We can use those resources to extract valuable minerals for our independence.”
Those minerals would come at a critical moment. The rare earth elements neodymium and dysprosium, in particular, are essential to the powerful magnets used in offshore wind turbines and electric vehicle motors. A recent report by the International Energy Agency projected that by 2040, the clean energy sector’s demand for these minerals could be three to seven times greater than it is today.
Related: Clean energy requires rare metals. Should we mine the ocean floor to get them?
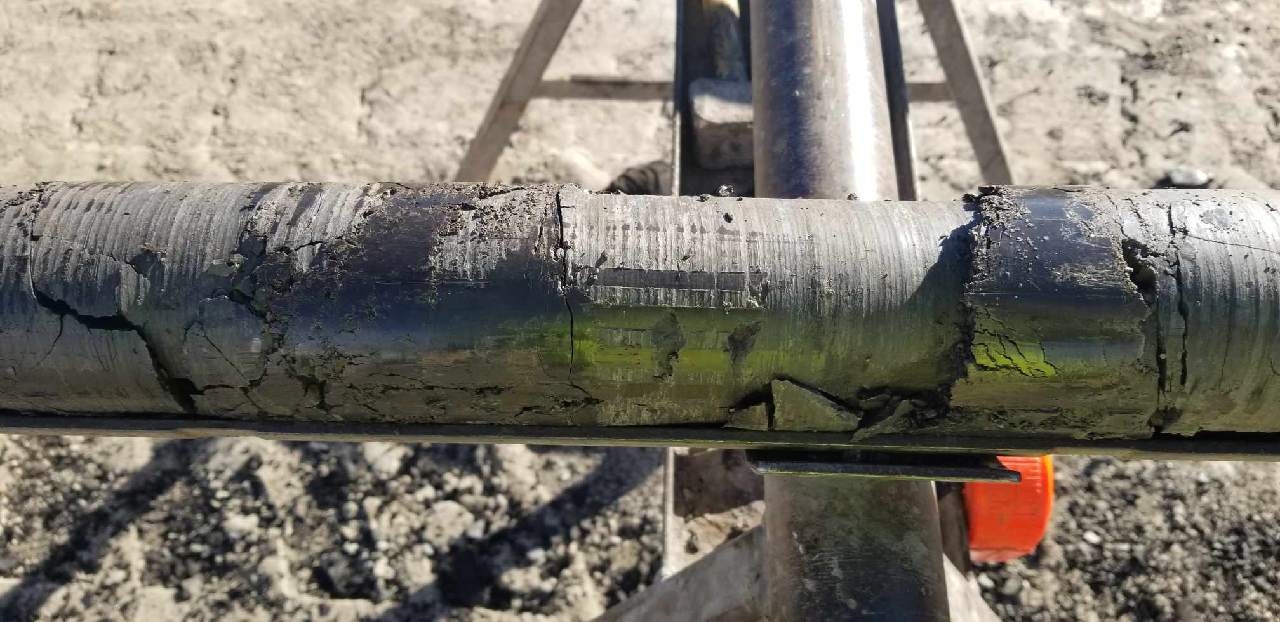
China currently dominates the rare earth market, accounting for 60 percent of rare earth mining and 90 percent of refining and magnet-making worldwide in 2019. For the Biden administration, which has promised that the clean energy transition will rely on products made in America, being reliant on a foreign adversary for a key component of our energy future is a problem. Another problem, however, is that conventional rare earth processing produces toxic and radioactive waste, taking a severe toll on human health and the environment.
Coal waste comes in a few different flavors. There’s coal ash, which is produced by coal-fired power plants. Today, there are more than 700 coal ash ponds and landfills scattered across 43 states, mostly in the eastern half of the country. Many of them are leaking dangerous amounts of toxic substances into groundwater, according to an investigation by Earthjustice. Coal mining produces other types of waste, including acidic, heavy metal-rich water known as acid mine drainage, as well as refuse piles of waste material buried near mines. Abandoned coal mines in need of cleanup can be found around the country, with the majority located in Pennsylvania, West Virginia, and Kentucky. The Bureau of Land Management estimates there are close to 5,200 abandoned coal mining sites yet to be fully reclaimed nationwide.
Extracting rare earths from this waste could help the U.S. meet a resource need while also solving an environmental problem. While the conventional rare earth ores mined today in places like China contain higher concentrations of these metals than coal waste does, the latter often contains relatively high concentrations of heavy rare earths, like dysprosium, which are harder to find in conventional ores. Scientists at the Department of Energy’s National Energy Technology Laboratory, who have been studying how to extract rare earths from coal waste since 2014, have already demonstrated that mixtures of them can be recovered at a “very high purity” in a laboratory setting, said Maryanne Alvin, the rare earth and critical minerals technology manager at the National Energy Technology Laboratory.
And while nobody knows exactly how much rare earth material there is hiding in coal ash piles, waste ponds, and acid mine drainage sites around the country, Alvin says that in the Appalachian region alone, an estimated 6,000 metric tons of rare earths flow through acid mine drainage sites each year. The United States’ annual rare earth demand stands at around 12,000 to 13,000 metric tons.
“Very rough estimates tell us if we could extract 100 percent of the rare earths from each of these types of refuse,” Alvin said, “we’d have a substantial amount of material that could be available for use.”
The DOE’s recent $19 million in funding aims to make those rough estimates more precise. Each of the research groups that received a grant will spend the next two years assessing the rare earth resources in coal deposits and coal waste products in a different part of the country, as well as figuring out how to get local businesses and industries plugged into a rare earth-from-coal supply chain. If the initial findings are promising, projects will receive additional funds to start implementing their plans through new pilot plants, innovation centers, and workforce training. In total, the DOE plans to allocate $122 million to the effort over 10 years. Scott Quillinan, the director of the Center for Economic Geology Research at the University of Wyoming, which received two of the 13 grants, thinks that’s a realistic timeline for bringing this nascent technology to commercial readiness.
“I think we need about three years to develop the technologies and prove them in the field, and then a couple of years to scale up to demonstration scale,” Quillinan said. “So I think you’re looking at about the five- to seven-year time scale for commercial deployment.”
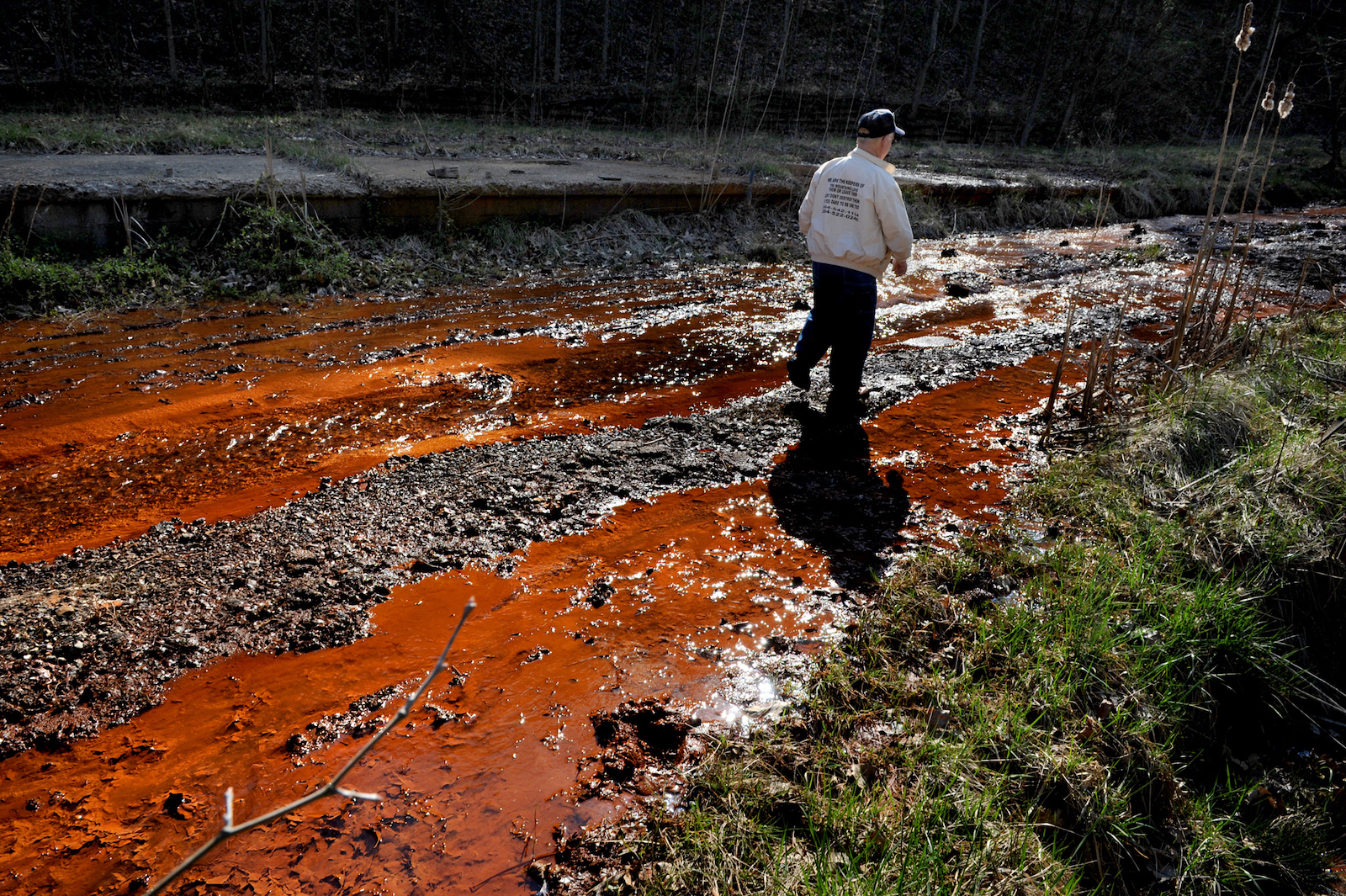
However, there are still many hurdles to overcome before we’ll be able to transform the nation’s coal ash piles into commercial, large-scale rare earth mining operations. First, scientists need to identify the most promising places to extract rare earths — no easy task, given how much variation there is across the thousands of different coal waste sites nationwide. They also need to develop cleaner and more efficient processes for separating and purifying the individual rare earths of interest. “That is a major challenge right now,” Pisupati, of Penn State, told Grist, noting that current separation techniques are “very expensive,” in addition to using a lot of acid and other caustic chemicals.
“We need to find environmentally friendly ways to do this,” says Stephan Oborny, a scientist with the Kansas Geological Survey who’s involved with one of the new research efforts led by the University of Kansas Center for Research. “That’s the tough part.”
If cleaner extraction methods can be developed, though, pulling rare earths out of coal waste could have environmental benefits. Alvin says it would make “total sense” to fold rare earth extraction into a larger effort to clean up a coal mine, using a portion of the revenue from rare earth recovery to help pay for remediation.
“We’re already actively reclaiming a lot of these abandoned mine sites,” said Virginia McLemore, the senior economic geologist for New Mexico’s Bureau of Geology and Mineral Resources. “If it should be that rare earths are in those wastes, then it becomes attractive.”
Aaron Mintzes, a senior policy council at the environmental nonprofit Earthworks, believes that there is “potential” to source minerals like rare earths from coal waste because there are already robust laws and policies in place to support its cleanup, including a requirement that the polluter pays a fee into a mine reclamation fund. However, Mintzes said he would also like to see more focus on recycling rare earths from technology, both to reduce demand for mining and prevent these minerals from winding up in landfills. Fewer than 1 percent of rare earths are thought to be recycled today. “Rare earths are really under-recycled in this country and only a modest increase in the recycling rate could have a really big impact,” Mintzes said.
The good news is developing methods of recycling rare earths from cell phones and extracting them from coal waste aren’t such dissimilar goals. “Frankly, there are relatively similar problems,” said Eric Shelter, a chemist and the director of the Center for Sustainable Separations of Metals at the University of Pennsylvania. “If you make a real breakthrough in the concentration of rare earths away from coal and coal byproducts, you could use that in technology as well.”
Places like Gillette, at least, are ready for that breakthrough. Over the last decade, coal production in Campbell County has declined more than 40 percent as cheap natural gas, and more recently, cheap renewables, have taken over the energy market. The coronavirus pandemic saw coal demand fall even further. As coal demand declines, a key source of revenue for mining communities is drying up. But those communities aren’t willing to fade into irrelevance, says Jim Ford, an energy advisor for the Campbell County Commission, where Gillette is located, who is spearheading efforts to manufacture advanced products, like activated carbon, from coal.
“Thermal coal’s had a good run,” Ford said, referring to burning coal for energy. “But things change. And there is a widespread acceptance here of saying ‘hey, if we want to remain valid in the eyes of the rest of the world and the rest of the country, we’ve got to change too.’”
